Integrate the numerous sources of reliability information
to eliminate in service failures, extend operating life
between failures and manage asset reliability.
Tango™ Reliability Information Management standardizes, integrates, communicates, and analyzes a facility's reliability information
to creating accountability, insuring that proper procedures are taken to repair or eliminate failures and reduce costs.
Tango™ provides a variety of services to customize a solution for your facility.
Equipment Management,
Condition Management,
RoundsLogging,
Repair Tracker, and
Oilography provide the best possible coverage to manage your Reliability Information.
Some of the many features provided by Tango™ include: Lifecycle Tracking, Condition Management Programs, Integrated Condition Reports,
Task Management, Equipment Management Programs, Physical Inspections, Vibration Analysis, Root Cause Failure Analysis, Repair Analysis,
Repair History, Asset & Warranty Information, Oil Analysis, Oil Sample Management, Test Result Sharing, and Repair/Test Status.
|
|
|
|
|
Tango™ Reliability Information Management standardizes, integrates, communicates, and analyzes a facility's reliability information to creating accountability, insuring that proper procedures are taken to repair or eliminate failures and reduce costs... read more. |
Tango™ Mobile was designed so that users could access this information from anywhere, as long as there is a phone or Wi-Fi signal present... read more. |
Tango Repair Tracker™ provides a web based portal where repair shops enter repair and failure details for industrial equipment that they service, which benefits both the facility and repair shops in many ways... read more. |
Oilography™ provides systematic oil sample analysis management for Industrial facilities. Oilography's™ web based approach provides easier schedule management, fast data review, and powerful interactive reports... read more. |
Condition-based maintenance implies the use of high-tech monitoring systems such as vibration analysis, infrared thermography, or oil analysis by specialized maintenance technicians or contractors... read more. |
With all the effort going into predictive maintenance (PdM) and asset management (EAM/CMMS) solutions, it is easy to overlook the
fundamental role of reliability information management (RIM). For many, RIM is a completely unfamiliar concept, but is the glue
that holds successful reliability programs together.
RIM is focused on bridging the gap. It consolidates asset condition data so it can be properly analyzed, understood, and pushed into
the workflow with the appropriate notifications. It captures feedback from the plant floor on what does and doesn't work in order to
continually improve the outcomes. And, it ensures that each condition is followed through to resolution.
Here are a few of the best practices.
Consolidate on
a Single Database
Manage Information,
NOT Raw Data
Track BOTH, Location
& Equipment Reliability
Manage Condition
Monitoring Tasks Efficiently
Integrate
Walk-Around Inspections
Use an Integrated
Status Dashboard
Establish a Repair
Vendor Interface
Identify
Bad Actor Locations
Maintain
Avoided Cost Records
Track Basic Metrics of
Your Reliability Program
Tango Reliability Information Management is used at Fortune 500 industrial manufacturing plants by technicians,
planners, engineers, supervisors, and managers as well as by contractors providing condition monitoring and
equipment repair services for those plants.
Tango is in use at over 250 facilities.
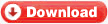
Our PowerPoint slide show!
Tango Version 13 is now available. To preview the new version or have a guided tour, please contact us.